The ABCs of Metal Roofing and Siding Finishes – Part 2
You don’t need to be an expert in metal to be able to specify the right items for your project, but a bit of expert advice is a good thing! Read on to learn part 2 of the crucial tips and information about painted metal you need to know!
Q6 – What should one know about corrosion-resistant finishes?
A – Corrosion resistant finishes include the metallic coating, the paint itself and additional paint layers such as primers and clear coats.
The metallic coating is applied to the steel before it is painted. This provides long-lasting corrosion resistance. It is called a metallic coating as the protective barrier is made up of a mixture of metals. The two common types are galvanized (comprised of 100% zinc) and Galvalume®/ZINCALUME® (a mix of aluminum and zinc). Zinc forms a sacrificial barrier to corrosion but is gradually consumed over time. Galvalume by comparison offers sacrificial and protective qualities which slow the rate of corrosion providing a longer service life.
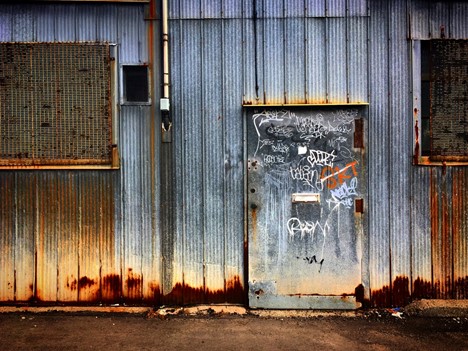
Inconsistent corrosion on untreated metal
Paint also works as an effective barrier to corrosion by encasing the base steel. Almost all pre-painted metal for exterior use has a primer layer underneath the topcoat, or color coat. These primers are specifically formulated with corrosion inhibiting pigments. High end paint systems such as PVDFs, due to their superior chemistry offer greater corrosion resistance. In more corrosion prone environments, such as those in close proximity to salt water, a thicker application of paint (such as a high build primer and thicker topcoat) or the additional layer of a clear coat over the top coat, can provide additional corrosion performance and warranty coverage. It is always best to discuss the environment of your project with a contractor or metal product manufacturer to ensure the correct finish is selected.
Q7 – What are micas and metallic colors?
A – Micas are specially formulated pigments that are added to the paint to create a sparkling or light catching effect. Historically this was achieved by adding metal flakes to a paint mix. Today, mica pigments are predominantly used in modern paint as they are more durable and do not require the paint system to include a clear coat like a traditional metal flake paint system. The majority of pre-painted metal products use micas but they are often labeled as metallics for ease of reference. Pearlescent or shifting colors typically use multiple mica pigments to create a distinctive color changing aesthetic.
The key consideration with Micas or Metallics is that they are batch and direction sensitive. Due to the shape and size of the pigments, there is very slight, uncontrollable variation from batch to batch. While relatively indistinguishable in isolation, the difference is apparent when installing different color batches directly next to one another.
To avoid this, always source sufficient material at one point in time from a single supplier. Sourcing additional material for job site mistakes or potential add-ons at a later date can result in color variation. These products will usually feature directional arrows on the strippable film to enable panels to be installed in a consistent direction.
Q8 – What about gloss and sheen?
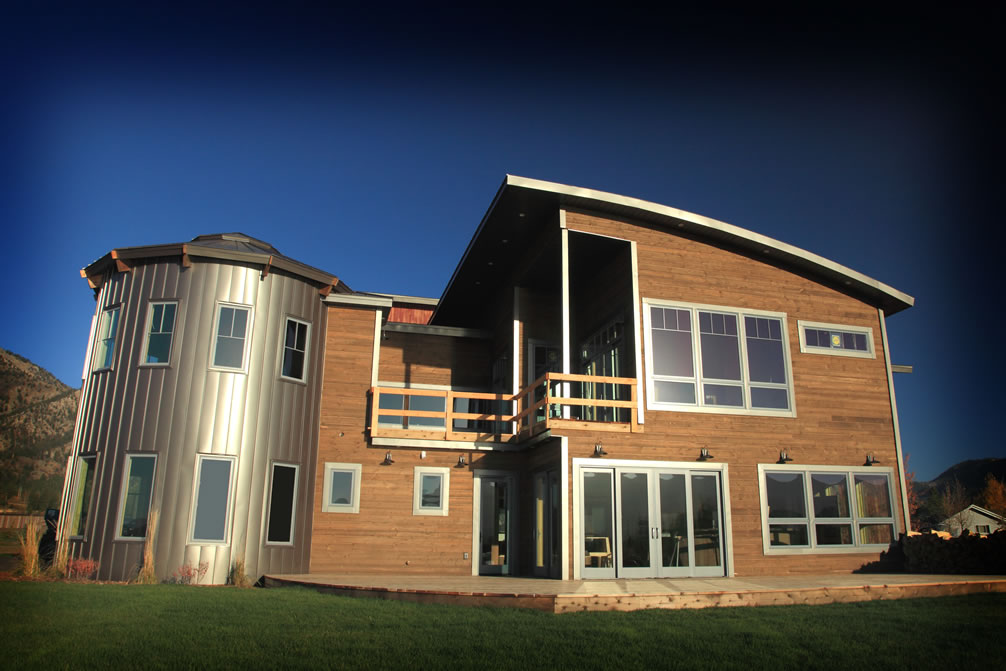
The sheen of our Vintage® Finish on residential siding in the sunlight.
A – Gloss and sheen are two aspects of the same topic, that is the visible ‘shine’ observed on a surface, created by the mirror-like reflection of light. The key difference between gloss and sheen is the way that it is observed.
Gloss is measured based on the reflection of the light source when observed at a 60-degree angle from the surface whereas sheen is observed at an 85-degree angle. The 85-degree angle is observed more in-line with the painted surface and can be a more accurate measurement for low gloss surfaces.
Both gloss and sheen can be accurately measured using a calibrated device called a gloss meter, with results reported in the format of gloss units (GUs), whereby 0 represents a perfectly matte surface.
Most standard painted metal products are in the 20-35 GU range with different manufacturers offering different low gloss and matte options.
Designers should be careful with the term ‘matte’, it is often used simply as a descriptive word, rather than a true indication of gloss. Readers should compare surfaces based on objective gloss units.
Q9 – How about coating textures?
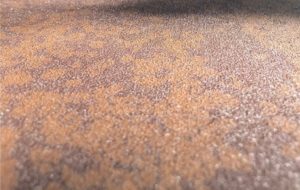
The texture of Rustic Rawhide
A – Today many advances have been made expanding the ability to achieve texture on metal. Texture can be imparted through adding particulates or through specially developed paint chemistry. Some paints crinkle when they cure to create a surface texture. These textures are similar to stucco or sandpaper
Most of these are specifically developed so that they offer a sensory experience without any performance detractors such as a fragile surface or a surface that attracts dirt and grime.
Texture does not necessarily need to be physical texture; multi-layered paint patterns can create the sense of texture through additional viewing depth. Or some paint technology includes both multi-layered paint patterns and texture for a truly stimulating painted surface.
Painted products can also be embossed to add additional texture. Embossing physically rolls a pattern into the metal. Common patterns include stucco and wood. This is often used for large flat unformed surfaces such as walk in cooler liners and appliances.
Q10 – What should you look for in coating warranties?
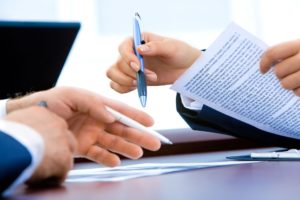
It’s important to look at the details of any warranty.
A – Coating warranties are often one of the most misunderstood elements by end users. The most important thing users must do is to review the warranty being offered before making a finish choice. Warranties are often marketed based on a headline number such as ’30 year’ – this can mean a lot of different things with warranty coverage varying by the type of paint system selected.
Headline warranty numbers, such as ’30 years’ typically refer to the integrity of the painted finish – that is it won’t lose adhesion, crack, or deform for the indicated period. The warranty duration for color fade or chalk may be something different. Further, the amount of color fade or chalking allowed within a set duration may vary between paint systems and suppliers (chalking is the creation of a white chalk like substance as the pigments of the paint break down due to UV exposure).
Often warranties will provide a table of coverage depending on the environment and severity of exposure to elements such as corrosion and industrial exposure. These environments will typically have a reduced coverage period.
Other key warranty considerations include:
Coating warranties usually do not cover the water tightness, workmanship of the installed solution or corrosion of the substrate.
Keeping the metal surface clean and free of debris through periodic cleaning will also help avoid damage that may not be covered by the warranty.
Non-uniform changes in appearance that result from uneven exposure to light (conditions created by the environment or building design such as trees) are typically not covered by a warranty.
Q11 – What are Cool coatings?
A – ‘Cool’ coatings utilize infrared (IR) reflective pigments that have been altered chemically and physically to reflect IR wavelengths whilst still absorbing the same visible light.
Near infrared (NIR) radiation is responsible for heat build-up within a structure. The purpose of IR reflective or cool pigments is to minimize heat build-up and reduce cooling costs. Most dark pigments readily absorb IR radiation and get hotter than lighter pigments; but when cool pigments are used, a dark color can offer ‘cool’ reflective properties.
The best way to evaluate how ‘cool’ a color is to review the SRI index. Solar reflectance (SR) is the amount of solar radiation reflected off a surface. Emissivity is the amount of heat a surface can dissipate away from itself. The solar reflectance index (SRI) is the consolidated value calculated from solar reflectance and emissivity with factors such as air flow considered. The higher the SRI the more reflective the coating.
A benefit of cool metal coatings is that the aged SRI value (its reflectance properties once installed) deteriorates very little over time. This contrasts to other materials such as asphalt, TPO or tile which attract and accumulate dust and dirt, reducing this reflectivity. Metals reflectivity performance can remain unchanged for 20 years or more.
To learn more about our metal colors, download one of the Steelscape Design Guides, explore our Range of Premium Finishes or Visualize online using our 3D visualizer.
Did you find this article helpful?